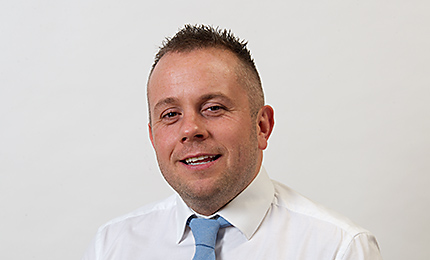
Author: Neal Hiscock,
Application Manager, Condair plc
Installing humidifiers - a contractor's guide
As humidifier specialists, we often see humidifiers that have been supplied as per the specification, installed perfectly and correctly commissioned but still cause their end-users problems. This is often due to the specification not fully meeting the end-user’s requirements and can be avoided by asking few questions at the outset to reaffirm the spec.
Typical information needed for correct humidifier selection includes:
• What level of humidity is required?
• What tolerance of humidity control is acceptable?
• What energy source is available and is there enough?
• Is energy cost or carbon footprint an important consideration?
• What maintenance costs are acceptable?
By exploring which features are really important to the user, there is often the opportunity to increase the value of the project. For instance, by considering energy savings or carbon footprint, the installation of an initially more expensive system may pay for itself in one year when the running costs are taken into account by the end-user.
Common errors
A very common problem that occurs with steam humidifier installations is incorrect condensate handling. When dealing with steam, careful attention has to be paid to where the condensation will flow to. If condensation is allowed to build-up in sags, kinks or long horizontal runs of pipe, it will encourage more condensation. This will affect the amount of steam the unit produces and lower the efficiency and output of the unit, resulting in a correctly specified unit not being up to the job.
Another important issue is the positioning of the humidifier. Humidifiers need to be serviced and access to the unit must be considered when the unit is installed. Too high and it may need two engineers to service it instead of one, doubling the cost. Too close to walls or the floor and it may be impossible to open electrical panels or install correct drains.
Hygiene must also be considered by the contractor when installing a humidifier. Good pipe design is needed to avoid dead-legs and water traps that could potentially harbour stagnant water. Also it is the contractor’s responsibility to inform the client of necessary maintenance in connection with the system. If there is a problem later on due to a lack of maintenance, the contractor may be considered to have breached their duty of care to the client by not informing them.
Controls & commissioning
Effective communication is vital to achieving a good controls strategy for any humidification system. For instance, if an energy efficient cold water system is to be used then the air may need to be preheated in order to achieve the correct temperature after humidification. Issues such as this need to be discussed at an early stage with the AHU supplier, controls company and humidifier supplier, otherwise there maybe some nasty surprises waiting to be discovered at commissioning when the system doesn’t do what it is designed to do.
It is strongly recommended that the humidifier manufacturer or supplier carry out the commissioning, as they are best placed to correctly set the system up. A quality humidifier supplier should be able to offer this service. Scheduling-in the controls company to be on site at the same time as the commissioning engineer will further enable swift and accurate set-up of the system and reduce performance problems later on.
Servicing
All humidifiers need to be maintained and this presents another opportunity for the contractor to provide a better service to the end-user whilst increasing profits from a humidifier project. Condair offers Planned Maintenance Agreements, whereby a schedule of service visits is arranged based on the operating parameters of the system. By introducing this type of service contract to the end-user at the installation stage of the project, the contractor can be making money on every humidifier project he handles years after the initial installation. This type of support can be offered by Condair on a subcontracting or commission basis to the installing contractor.
Contractors have the opportunity to approach the question of servicing at an early stage with the end-user, as it’s important to ascertain whether or not the system can be taken offline for essential maintenance. Some process industries require consistent humidification 24/7 to maintain effective production. If the humidifier cannot be shut down then the initial project ought to involve a back-up unit, which presents another opportunity to up-sell the project, thus increasing end-user satisfaction whilst adding profit to a job.
Good advice
The most important thing to remember when setting out on a humidification project is to get good advice from a competent supplier. From product selection to servicing, there are often opportunities to up-sell to improve customer satisfaction and many common errors to avoid along the way. A quality humidifier supplier will work alongside the contractor to help them make the most from each project.
Things to specifically look for in a supplier include a comprehensive range of CE and WRAS approved products, a service department that offers support and advice on installation, commissioning and servicing, and quality standards such as ISO and Investors in People.